Research
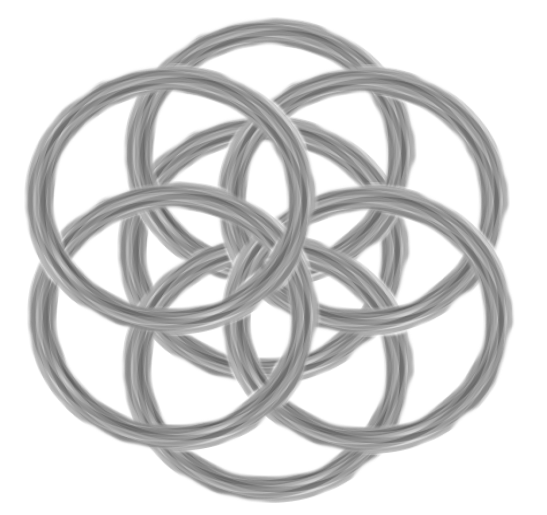
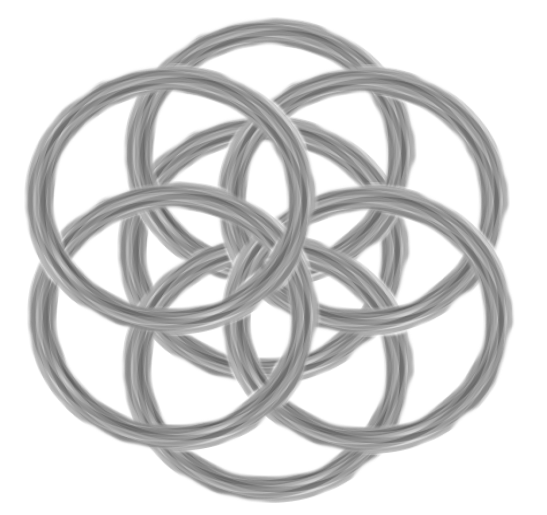
Interdisciplinary research on studying the physical, chemical, and biological interactions between tailored and engineered surfaces and their surrounding thermal, fluidic, and particulate environments
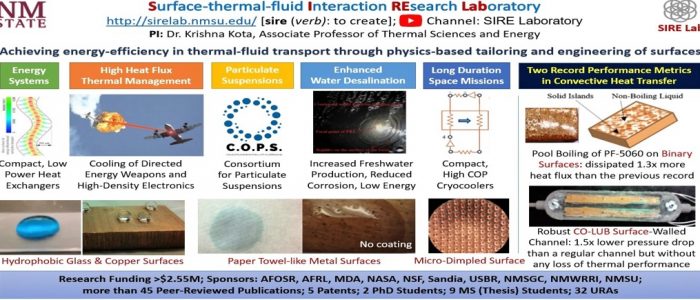
Surfaces are omnipresent. The interaction of any material or object or being, either living or non-living, with its surrounding environment is through a surface. The predominant focus of our interdisciplinary research is on studying the physical, chemical, and biological interactions between surfaces and their surrounding thermal, fluidic, and particulate environments with the goal of achieving technological performance enhancements and societal benefit, e.g., the interaction of a hot electronic or heat sink surface with a coolant, the interaction of surfaces with virus particles or infectious aerosols, the interaction of filtration surfaces with particulates, or the interaction of human skin or a water desalination surface with its surrounding environment. So far, our research has demonstrated notable benefits in the following application areas.
1. Energy and Thermal Management: Energy-efficiency in convective transport, heat exchangers, cooling of high density electronics and photonics, directed energy weapons, portable devices, buildings, thermodynamic cycles, portable and distributed power, thermal energy storage, waste heat recovery
Our research in this area was/is funded by AFOSR, AFRL, MDA, NSF, and Sandia.
2. Health: Particulate suspensions in air and water, airborne and fomite transmission of pathogens, enhanced water desalination, air and water quality, filtration and separation
Our research in this area was/is funded by US Bureau of Reclamation, NM-WRRI, NMSU, and DOE.
3. Space Transportation: Long-duration space missions beyond low Earth orbit, portable cryocoolers, compact heat exchangers, propellant management and zero boil-off, cooling of air/spacecraft electronics
Our research in this area was/is funded by NASA and NMSGC.
We have tailored and engineered both metallic and non-metallic surfaces using a variety of scalable micro-/nano-manufacturing approaches such as metal and polymer additive manufacturing, bulk micro-manufacturing or wet etching, micro-milling, micro-cold forming, rapid prototyping, diffusion bonding, and surface patterning.
A word cloud of some of the novel surfaces that we created, designed, and/or analyzed hitherto.
Focus
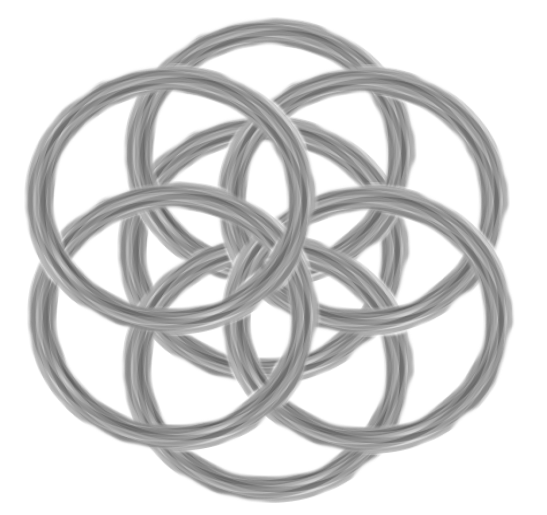
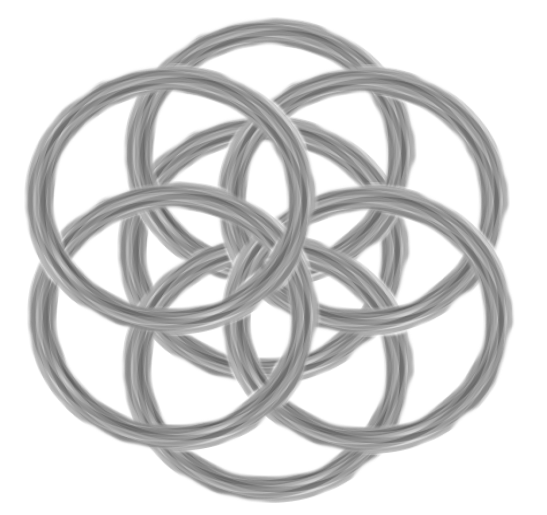
Fundamental study of enhanced/altered single-phase and two-phase thermal-fluid transport phenomena on surfaces with tailored roughness and/or geometrical features
Whether the goal is to achieve energy independence or enable cost-effective renewable energy technologies or reduce global warming by decreasing anthropogenic carbon emissions, or enhance defense/security systems, achieving major gains in energy efficiency in the constitutive processes is one of the most economical and effective ways.
In simple phraseology (by the American Physical Society), energy efficiency denotes the ratio of useful energy or work a device produces to the energy the device consumes. Conjugate thermal-fluid transport can be deemed energy-efficient if the extracted/transported thermal energy exceeds the mechanical energy expended for accomplishing the said transport.
Our goal is to realize dramatic energy efficiencies in convective transport at all length scales by employing tailored surfaces and bio-inspired designs. We use numerical and/or experimental techniques to conduct our research for gaining a fundamental understanding of thermal and momentum based interactions of fluids with surfaces of altered topology and/or morphology. Our highly interdisciplinary research enables us to work with collaborators in the areas of materials, manufacturing, chemical engineering, civil engineering, chemistry, electrical and electronics engineering, computation, statistics, biology, and MEMS/NEMS.
Some of the tailored surfaces that we designed, created, and/or analyzed for enhancing single-phase and two-phase convective transport include:
We are currently focusing on the following research topics/projects:
Binary Surfaces (BiS) for enhanced boiling heat transfer (supported by USBR & NM WRRI and NMSU): Robust BiS were prepared on copper using a facile, scalable bulk micro-manufacturing approach. Boiling experiments were carried out using a dielectric liquid, PF-5060, to obtain the maximum heat flux limit and the heat transfer coefficient (HTC) from the measured temperature data. It was observed that, compared to a smooth/plain copper surface, a BiS was able to simultaneously enhance the maximum heat flux limit by ~2.2 times. A maximum heat flux of 35.06 W/cm2 was recorded, which is higher than the enhancements reported so far in literature for the pool boiling of PF-5060 on any enhanced surface.
Fundamental science question and motivation: Can the CHF limit for boiling heat transfer of liquids on a surface be pushed beyond state of the art using robust, scalable surfaces by overcoming the current limitations on surface wetting and vapor bubble removal at the same time?
BiS is a unique solution which have the potential to push the CHF and HTC values beyond the current state of the art. These surfaces promote wetting to the dry zones while simultaneously providing scope for early departure of vapor bubbles. For more information, watch the video at: https://www.youtube.com/watch?v=GHd8xhPQlOg
Two-phase thermal management of directed energy weapons (supported by AFRL and MDA): A 1 kW laser diode is loaned by AFRL to NMSU for carrying out this project through an Education Partnership Agreement between NMSU and AFRL. Two-phase thermal management solutions based on robust, scalable surfaces with tailored micro-nanoscale roughness features will be tested in this effort to handle the ultra-high heat densities generated by the laser diode.
For more information on the methodology employed, please visit our past research work (link located at the end of this page) on “A Novel Integrated Vapor Chamber – Thermal Energy Storage System.”
Robust Conducting-Lubricating (CO-LUB) surfaces for simultaneous pressure drop reduction and heat transfer enhancement (supported by NSF and NMSU): In this effort, forced convective performance of a dielectric liquid (mineral oil) was numerically and experimentally analyzed in a channel with two Conducting-Lubricating (CO-LUB) surface walls. A simplified two-dimensional model was developed to simulate single-phase forced convective flow of mineral oil in a channel with two CO-LUB side walls using ANSYS FLUENT software. The key finding of these simulations is that the CO-LUB surface acts as the high thermal conductivity lubricating layer which aided in both pressure drop reduction and heat transfer coefficient enhancement. Such reduction in pressure drop accompanied by a simultaneous increase in the heat transfer coefficient was rarely reported before. A facile, low-cost, and scalable bulk micro-manufacturing approach was used to prepare the CO-LUB surfaces and forced convection experiments were performed in a channel with these surfaces to verify the key finding of the numerical simulations.
Fundamental science question and motivation: In forced convection heat transfer, any attempt to improve heat transfer would almost always results in increased pressure drop and any attempt to decrease pressure drop always results in decreased heat transfer (Reynolds-Colburn Analogy). Can pressure drop reduction and heat transfer enhancement be realized at the same time?
The answer lies in using CO-LUB surfaces, which act as the high thermal conductivity lubricating layers that aid in both pressure drop reduction and heat transfer coefficient enhancement at the same time.
Microchannels with wavy surfaces for enhanced thermal performance in cryogenic heat exchangers (supported by NASA/NMSGC): In this effort, a split wavy channel heat recuperator design was pursued to overcome the technical show-stoppers of current cryogenic heat exchangers. A split wavy channel design has the advantage of increased flow length and improved heat transfer in the same form factor as a heat exchanger with straight channels without causing a large increase in the pressure drop. So far, this concept has never been studied and exploited for a cryogenic heat recuperator. High fidelity numerical simulations were employed to study the three-dimensional flow of working fluid through hot and cold wavy channels of the heat recuperator separated by a wall. Performance of various wavy configurations was compared using a performance factor, and traditional heat exchanger effectiveness. The results showed that wavy channels, due to a unique fundamental physical phenomenon of geometry governed boundary layer thinning, help in augmenting heat transfer and in realizing a high-effective (>0.98), compact (than any current state of the art) cryogenic heat exchanger.
Fundamental science question and motivation: Low Reynolds number internal/channel flows, which have numerous applications, are usually laminar. Any attempt to improve heat transfer by flow mixing or separation would almost always results in increased pressure drop. Can heat transfer be augmented at low Reynolds numbers without flow mixing and the associated rise in pressure drop?
Dr. Kota is instrumental in fundamentally studying the flow characteristics in wavy microchannels at low Reynolds numbers (10 to 200) and observed through numerical simulations and flow visualization that it is possible to obtain significant heat transfer augmentation without causing any mixing in the flow. These seminal results are attributed to boundary layer thinning and squeezing effect in microchannels with wavy walls. Other key personnel who were previously involved in this work are Prof. Liang Gong (China University of Petroleum), Prof. Wenquan Tao (Xi’an Jiaotong University), and Prof. Yogendra Joshi (Georgia Tech).
Variable gravity flow boiling (in collaboration with AFRL and NASA/NMSGC): On this project, Dr. Stochaj and Dr. Kota have been supervising freshmen as an experiment program to see whether involving them in exciting engineering research projects at an early stage would improve their retention. Dr. Hynes of NMSGC helped with the funding. Dr. Kota’s current graduate student, Josh Budish, guided these freshmen on design, building and launching a compact flow boiling heat transfer experiment in a sounding rocket in July 2016 from Alamogordo, NM. All the freshmen decided to continue in engineering (100% retention). A few of them are now still working on this project. They are working on improving the flow boiling loop and this time, thanks to NMSGC and guidance by Dr. Paulo Oemig, they will launch the experiment on a high altitude balloon (~100,000 ft) in August 2017.
In collaboration with the ACES College and CE department, we also work on enhancing heat transfer in buildings (supported by TRI), water desalination (supported by USBR-WRRI), and soil thermal characterization. In the area of boiling heat transfer, we recently worked on enhancing boiling using micro-dimpled surfaces in collaboration with Prof. Mohamed El-Genk at UNM.
Past research work on thermal energy storage, cryocooler development, and enhancing convection heat transfer using a variety of tailored surfaces.